湖南日报·新湖南客户端 2025-03-17 12:00:47
[来源:湖南日报 03版要闻 2025-03-17]
湖南石化破解困扰行业30余年难题,实现高浓度有机含盐废液零排放——
化工废液处理,有了通用“净水器”
湖南日报全媒体记者 周磊 通讯员 彭展
初春时节,中石化湖南石化公司年产60万吨己内酰胺产业链搬迁与升级转型发展项目SE水煤浆水冷壁气化装置区,银色管道蜿蜒延伸。管道内,己内酰胺废液被“点石成金”——它们不再是令人头疼的污染物,而是与原料煤混合,成为煤气化装置制浆的“新水源”。
操作员紧盯控制屏上的参数,煤浆浓度稳定在60%以上。一项项跳动的达标数据,诉说着一场化工与生态的“和解”。
运行1年多来,该装置已累计“吞下”己内酰胺装置产生的废液50多万吨,形成“以废养产”的循环模式,实现高浓度有机含盐废液零排放。
技术团队负责人宋星星颇为自豪:由他带领技术团队独创的己内酰胺废液与煤共气化技术,解决了困扰行业30余年的废液处理难题。
己内酰胺是尼龙工业的基石。过去,己内酰胺生产过程中产生的高浓度有机含盐废液需以传统浓缩焚烧法处理,不仅成本高,还产生二次污染。
“湖南石化己内酰胺产能大、质量好,市场竞争力强,但每年处理废液成本高。”宋星星说,早在2017年,他就开始关注研究废液与煤共气化处理技术,己内酰胺项目整体搬迁为技术落地提供了契机。
曾经,己内酰胺生产装置与岳阳市主城区紧密相连,距离长江不足1公里。
为破解“化工围江”困局,湖南石化将己内酰胺产业链整体搬迁到距离长江岸线3.1公里的岳阳绿色化工高新区,新建58套装置,实现产能倍增、污染物排放减半。
设计新建煤气化装置时,宋星星提出:“放弃传统的粉煤气化工艺,采用新型SE水煤浆水冷壁气化技术,用水冷壁代替传统耐火砖,提高使用年限,以己内酰胺废液替代新鲜水制浆。”
“从未有过前例,用废液怎么能产出合格的煤浆?”投资大、风险高,不少人提出反对意见。
“我们解决了废液中苯、氨、酸等成分的处理难题,并优化煤浆配方,使废液与煤完美融合。”宋星星以研究实验数据说话——煤浆要求浓度高、黏度低,一般两者呈正相关,但以废液代替清水后,可在提高煤浆浓度的同时降低黏度。
他在清华大学、华东理工大学等高校以及不同添加剂供应商处开展的实验结果,也佐证了研究结论。
2022年5月,SE水煤浆水冷壁气化装置正式开建。2023年12月,装置建成,投入使用。
“投产后出现了一点小意外。”宋星星说,本以为灰水系统呈碱性,没想到煤气化反应副产甲酸增多,灰水呈酸性,存在腐蚀设备的风险,他迅速带领团队寻找解决办法,添加烧碱,中和酸性。
一波未平,一波又起。生产时,本该留在煤气水洗塔中的清洗水,随着煤气夹带到下游变换单元,影响变换单元运行,煤气化装置只能以60%负荷运行。
“我们研究了一个月,发现煤气水洗塔固阀塔盘流通面积不够,需要增加一倍。”宋星星说,与供应商联系将其改造后,问题很快解决。
2024年二季度,该装置满负荷生产,在国内首次实现己内酰胺废液与煤共气化技术的工业应用。
“节省成本就是增加效益。”宋星星给记者算了一笔账:煤气化装置每年可资源化利用己内酰胺废液40万吨,节约废液处理成本近4000万元,减少制浆用新鲜水40万吨,减少新鲜水成本100万元。
从“排废”到“吞废”,从“环保包袱”到“效益源泉”,一场绿色变革,在银塔林立的厂区悄然兴起。
2月28日,湖南石化橡胶部也将80吨含冷媒废水输送至煤气化装置磨煤机中,实现“变废为宝”。
“以往含冷媒废水处理成本每吨2000元。”宋星星笑称,这套装置如同通用“净水器”,可以治愈传统化工废液的污染顽疾。
责编:王相辉
一审:吴天琦
二审:徐典波
三审:姜鸿丽
来源:湖南日报·新湖南客户端
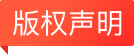
版权作品,未经授权严禁转载。湖湘情怀,党媒立场,登录华声在线官网www.voc.com.cn或“新湖南”客户端,领先一步获取权威资讯。转载须注明来源、原标题、著作者名,不得变更核心内容。
我要问